The mining industry is reliant on disclosing mineral resources and reserves to investors to demonstrate value and secure capital to bring new mines into production. Reporting codes have evolved to protect investors. Security exchange commissions require (1) mineral resources to be classified into measured, indicated and inferred, and (2) ore reserves to be classified into proven and probable. These bins depend on many factors, but my concern here is geological uncertainty in the tonnage (quantity) and grade (quality) of the material that may be mined. Geological uncertainty exists given geological variability at all scales and relatively sparse sampling.
Geostatistical and probabilistic tools have evolved to quantify geological uncertainty. As trust in the reliable quantification of uncertainty grows, it is tempting to depend on measures of uncertainty for classification. We often hear that measured resources will have the mined quarterly tonnage, grade, and metal within 15% of predicted with a 90% probability or higher. Indicated resources have annual tonnage, grade, and metal within 15% of predicted with a 90% probability or higher. These measures of uncertainty are necessarily subjective and must be reconsidered for each deposit – what is applicable to a narrow epithermal gold deposit is very different from a high throughput porphyry deposit. Nevertheless, there is an allure to depend more on an objective analysis of uncertainty.
This author advocates strongly for classification to be based on geometric criteria such as drill hole spacing instead of direct measures of uncertainty. Where possible, the drill hole spacing thresholds for classification should be supported by a quantification of uncertainty in tonnage, grade and metal for relevant production volumes, but direct consideration of uncertainty for classification should be avoided. This was articulated in a paper more than 15 years ago (Deutsch, C.V., Leuangthong, O., and J.M. Ortiz, A Case for Geometric Criteria in Resources and Reserves Classification, SME Transactions Vol 322, December 2007). Additional modern concerns have emerged. This is an opportunity to review the primary reasons why classification directly with uncertainty is not recommended.
The assessment of accurate and precise large scale production uncertainty requires a significant amount of professional effort. Geological boundary uncertainty, trend model uncertainty, parameter uncertainty, and data uncertainty must all be carefully considered within a well crafted conceptual geological model; otherwise, the uncertainty is likely too low. Resampling and resimulation are required to understand how the uncertainty responds to more drilling. The expertise for such advanced studies is limited. When possible, these studies should be undertaken and the results used to support decisions related to classification, but it would be unreasonable to expect such effort in all cases.
Considering monthly, quarterly, and annual production volumes seems reasonable, but (1) the production volumes are rarely clearly defined, (2) low grade material and internal waste confound the size of the production volumes, (3) there may be multiple mining faces in ore and waste, (4) there may be stockpiles, and (5) production may be comingled with that of other deposits. Nominal production volumes are reasonable to inform drill hole spacing, but not for direct use in classification.
The direct consideration of mineral resource uncertainty in classification would appear transparent, but it is not. Some measures of uncertainty would require unreasonably close drill hole spacing. Other measures may only require very widely spaced drill holes. The target uncertainty could be changed to get almost any drill hole spacing desired. This is not right. The number and spacing of the drill holes transparently discloses the data and professional judgement on geological continuity.
Why not use simulation or models of uncertainty for classification? The main reasons are (1) challenges in getting uncertainty quantified accurately, (2) the complexity of defining reasonable production volumes, and (3) the lack of transparency on the real data underlying the estimates. There are alternatives. The kriging efficiency is a dimensionless expression of the kriging variance, which relates to the quality of a block estimate. The kriging slope of regression measures how constrained the search must be to avoid excessive smoothing, which also relates to the quality of a block estimate. These methods involve a variogram model and kriging search plans, and are therefore subject to annual changes associated with user interpretation and estimation parameterization. This could lead in turn to significant changes in the classification of material and implied confidence, which is problematic. Meeting a specified search criteria could be used as a more stable alternative, but drill hole spacing is recommended as the most clear and simple method.
There are many advantages to using drill hole spacing as the foundation for classification. Drill hole spacing is consistent with most current disclosures. The calculation of drill hole spacing is clear and the results are easy to understand. It is straightforward to account for mitigating factors in the drill hole spacing calculation or by modifying the drill hole spacing requirements. When feasible, drill hole spacing and uncertainty studies should be used to support the chosen spacing. Regardless, the final spacing decision is ultimately subject to professional judgement on required confidence.

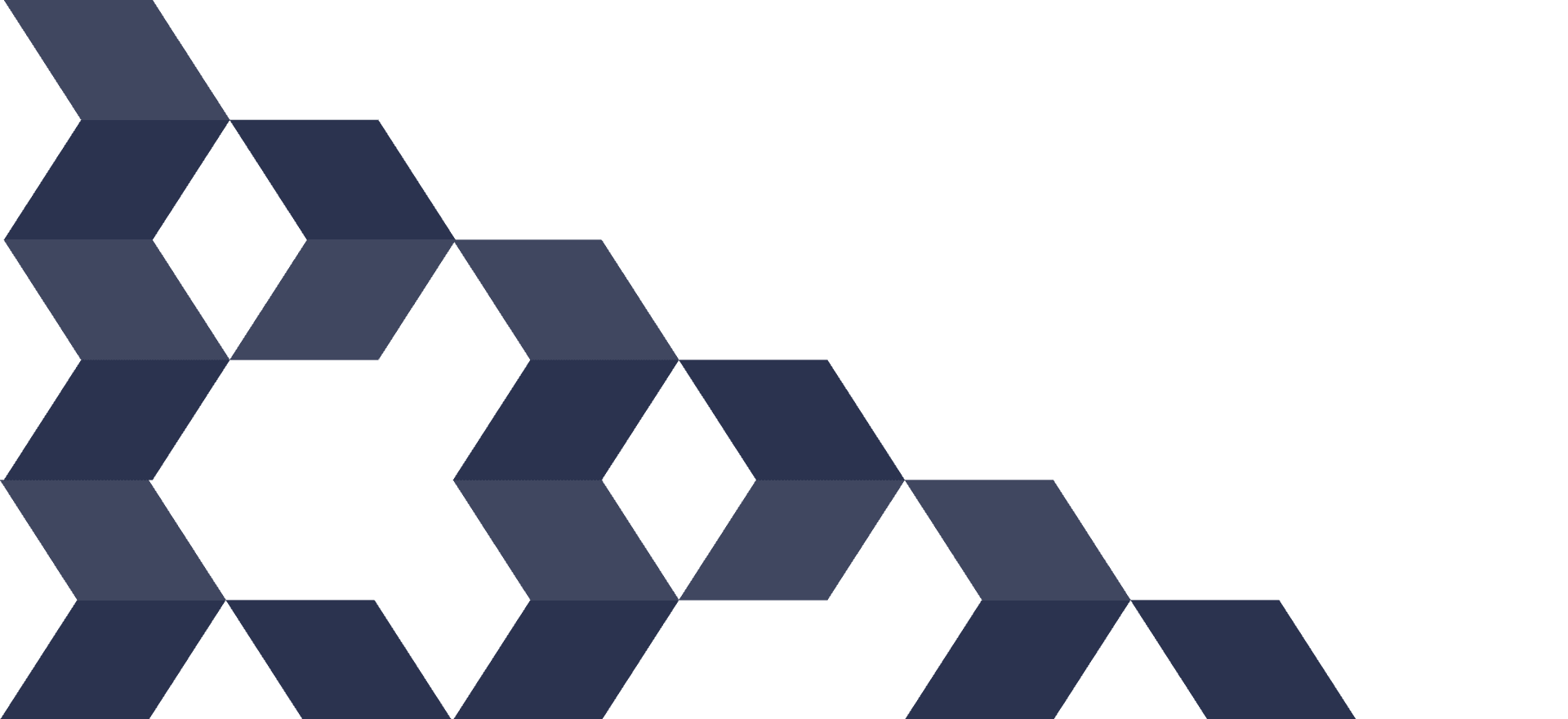